目前,工業(yè)上順酐的工藝路線按原料可分為苯氧化法、正丁烷法氧化法、C4烯烴法和苯酐副產(chǎn)法4種。下面
順酐廠家來講講順酐工藝的比較與選擇:
At present, the production process routes of maleic anhydride in industry can be divided into four types based on raw materials: benzene oxidation method, n-butane oxidation method, C4 olefin method, and phthalic anhydride by-product method. Below, maleic anhydride manufacturers will discuss the comparison and selection of maleic anhydride production processes:
以前,苯氧化法應(yīng)用為廣泛,但由于苯資源有限,C4烯烴和正丁烷為原料順酐的技術(shù)應(yīng)運(yùn)而生,尤其是富產(chǎn)天然氣和油田伴生氣的,擁有大量的正丁烷資源,因此近年來正丁烷氧化法順酐的技術(shù)發(fā)展迅速,已經(jīng)在順酐中占主導(dǎo)地位。C4烯烴氧化法因副產(chǎn)物較多已被淘汰,而苯酐副產(chǎn)法順酐產(chǎn)量有限。
Previously, the benzene oxidation method was widely used, but due to limited benzene resources, the technology of producing maleic anhydride using C4 olefins and n-butane as raw materials emerged, especially in countries rich in natural gas and oilfield associated gas, which have a large amount of n-butane resources. Therefore, in recent years, the technology of producing maleic anhydride using n-butane oxidation method has developed rapidly and has taken a dominant position in the production of maleic anhydride. The C4 olefin oxidation method has been phased out due to its high number of by-products, while the production of maleic anhydride from the phthalic anhydride by-product method is limited.
苯氧化法及正丁烷法是目前各國順酐普遍采用的工藝。我國主要采用苯氧化法,經(jīng)過多年的開發(fā)應(yīng)用,工藝比較成熟,同時(shí)具有工藝簡單、操作容易、投資省、收率高等特點(diǎn)。
The benzene oxidation method and n-butane method are currently commonly used processes in the production of maleic anhydride in various countries. China mainly adopts the benzene oxidation method. After years of development and application, the process is relatively mature, and has the characteristics of simple process, easy operation, low investment, and high yield.
順酐產(chǎn)品成本50%左右是原料費(fèi)用,已工業(yè)化的順酐技術(shù)都是以控制大收率來確定工藝條件。與傳統(tǒng)苯法相比,正丁烷氧化法具有原料價(jià)廉、污染小等優(yōu)點(diǎn)。
About 50% of the cost of maleic anhydride products is the cost of raw materials, and the industrialized production technology of maleic anhydride determines the process conditions by controlling the high yield. Compared with traditional benzene method, n-butane oxidation method has advantages such as low cost of raw materials and low pollution.
正丁烷法每噸順酐產(chǎn)品消耗1.l~1.2噸正丁烷,而苯法每噸順酐產(chǎn)品消耗1.1~1.3噸苯。而且正丁烷法順酐理論產(chǎn)量為1:1.69,苯法為1:1.256,因此正丁烷的順酐理論產(chǎn)量比苯法高許多。
The n-butane method consumes 1-1.2 tons of n-butane per ton of maleic anhydride product, while the benzene method consumes 1.1-1.3 tons of benzene per ton of maleic anhydride product. Moreover, the theoretical yield of maleic anhydride produced by the n-butane method is 1:1.69, and that by the benzene method is 1:1.256. Therefore, the theoretical yield of maleic anhydride produced by n-butane is much higher than that by the benzene method.
隨著技術(shù)的不斷發(fā)展,正丁烷作原料其單耗將比苯法低得多,正丁烷不僅消耗少,而且與苯法相比,其毒性也小,同時(shí)正丁烷法順酐對環(huán)境污染小,隨著全球壓力越來越大,正丁烷法在滿足要求以及發(fā)展前景方面比苯法更具有生命力。
With the continuous development of technology, the unit consumption of n-butane as raw material will be much lower than that of the benzene method. n-butane not only consumes less, but also has less toxicity compared to the benzene method. At the same time, the production of maleic anhydride using n-butane method has less environmental pollution. With the increasing global environmental pressure, the n-butane method has more vitality than the benzene method in meeting environmental requirements and development prospects.
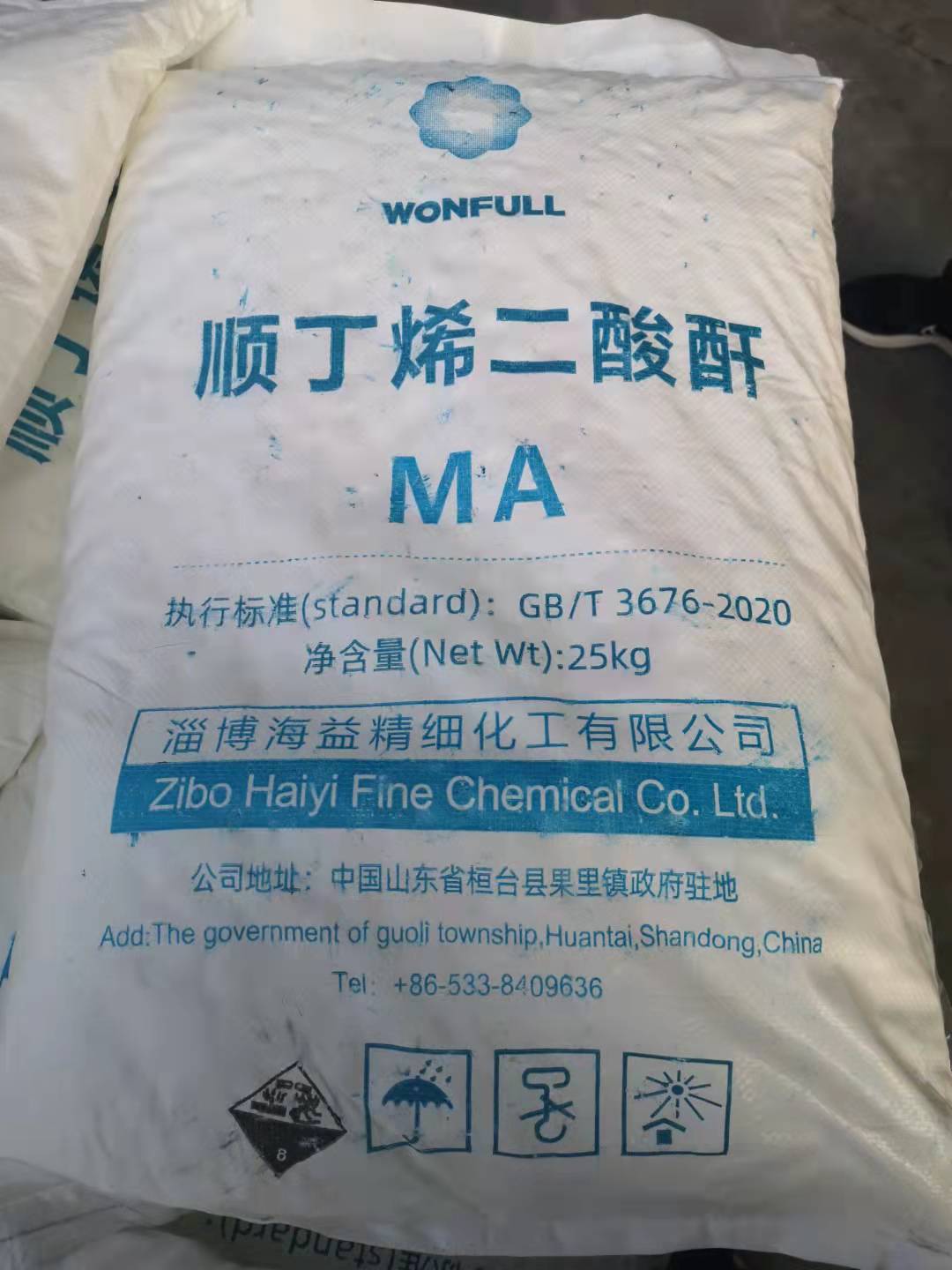
正因?yàn)槿绱?,目前全球新建順酐能力約80%采用正丁烷路線,而且還有不斷增加的趨勢。由正丁烷氧化制順酐,自1974年美國孟山都等公司實(shí)現(xiàn)工業(yè)化以來得到迅速的發(fā)展,丁烷來自煉廠氣、裂解氣或油田伴生氣等。
Because of this, about 80% of the global newly built production capacity of maleic anhydride adopts the n-butane route, and there is a continuous increasing trend. The oxidation of n-butane to maleic anhydride has undergone rapid development since the industrialization of companies such as Monsanto in the United States in 1974. Butane comes from refinery gas, cracking gas, or oilfield associated gas.
在固定床工藝中,由于正丁烷氧化選擇性和反應(yīng)速率均比苯法低,正丁烷-空氣混合物中正丁烷濃度可高達(dá)1.6%~1.8%(摩爾分?jǐn)?shù)),順酐收率按正丁烷計(jì)約為50%,故對于同樣規(guī)模的裝置需求較大的反應(yīng)器和壓縮機(jī);采用流化床反應(yīng)器可使正丁烷在空氣中的濃度提高到3%~4%(摩爾分?jǐn)?shù))。流化床反應(yīng)器傳熱效果好,且投資較少,但流化床用的催化劑磨損較多,對大型順酐裝置(2萬噸/年以上),如能獲得價(jià)廉且供應(yīng)有保障的正丁烷原料,宜選用流化床反應(yīng)器。
In the fixed bed process, due to the lower selectivity and reaction rate of n-butane oxidation compared to the benzene method, the concentration of n-butane in the n-butane air mixture can reach as high as 1.6% to 1.8% (molar fraction), and the yield of maleic anhydride is about 50% based on n-butane. Therefore, there is a greater demand for reactors and compressors for production units of the same scale; The use of a fluidized bed reactor can increase the concentration of n-butane in air to 3% to 4% (mole fraction). The fluidized bed reactor has good heat transfer efficiency and less investment, but the catalyst used in the fluidized bed is more worn. For large maleic anhydride production units (over 20000 tons/year), if affordable and guaranteed supply of n-butane raw materials can be obtained, it is advisable to choose a fluidized bed reactor.
目前正丁烷氧化工藝以固定床為主,順酐回收工藝除我國兩套裝置采用水吸收法,其他裝置均采用溶劑吸收法。溶劑采用DBP要多于DIBE。
At present, the n-butane oxidation process is mainly based on a fixed bed, and the maleic anhydride recovery process uses solvent absorption method except for two units in China that use water absorption method. The solvent uses DBP more than DIBE.
綜上所述,正丁烷氧化工藝后處理,溶劑吸收法具有產(chǎn)品質(zhì)量穩(wěn)定、裝置收率高、副產(chǎn)物少、腐蝕性弱、成本低、公用工程消耗小、蒸汽輸出平穩(wěn)且連續(xù)等優(yōu)點(diǎn),所以后處理工藝采用溶劑吸收工藝更經(jīng)濟(jì)、更,同時(shí)這也符合我國國情和環(huán)境政策的要求。您有需求就來我們網(wǎng)站
http://flyus.com.cn咨詢吧!
In summary, the solvent absorption method for the post-treatment of n-butane oxidation process has the advantages of stable product quality, high device yield, fewer by-products, weak corrosiveness, low cost, low utility consumption, stable and continuous steam output, etc. Therefore, the solvent absorption process is recommended for future treatment processes to be more economical and environmentally friendly, which also meets the requirements of China's national conditions and environmental policies. Come to our website if you have any needs http://flyus.com.cn Consult!